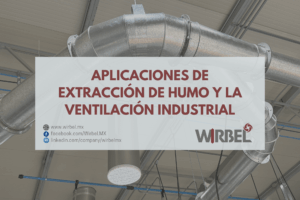
Gerente de Diseño y Proyectos
En el sector de fabricación industrial, los hábitos más sencillos pueden ser la clave para el éxito. Durante mis estudios universitarios y mis prácticas en una empresa de neumáticos, aprendí sobre la importancia de la filosofía de las 5’S en cualquier sector de manufactura. Experimenté cómo la aplicación de estas etapas se centra en un aspecto específico de la organización y la limpieza, y juntas forman un enfoque integral para mejorar la eficiencia y la productividad en el lugar de trabajo, dando resultados como la organización de manuales de máquinas y la claridad en los materiales disponibles, que condujo a resultados más limpios y una cultura laboral más ordenada.
He podido notar que esta filosofía muy pocas veces es aplicada en las empresas y que de implementarse podría significar un cambio decisivo para mejorar procesos de fabricación. Es por eso que me gustaría compartir las bases de cada etapa, para que con eso cada empresa pueda identificar cómo aplicarlo a su sector en específico.
El objetivo de esta primera etapa es categorizar los elementos en artículos necesarios y no necesarios. Esto implica identificar y eliminar cualquier artículo que no se utilice periódicamente y que no contribuya directamente al proceso de fabricación. Una acción concreta a realizar para señalar estos elementos es la colocación de Tarjetas Rojas colocadas en la ubicación en donde se identifica que hay un elemento estropeado, fuera de lugar o no identificado para poder así realizar una acción específica en un tiempo determinado; puede ser eliminar, reubicar o identificar.
Indicadores de mejora que pueden observarse:
Una vez que se ha completado la etapa de clasificación, es importante establecer un arreglo óptimo de los elementos restantes. Seiton hace referencia a organizar de manera sistemática los elementos necesarios en el lugar de trabajo para facilitar el acceso y la eficiencia. Esto puede implicar la implementación de emplazamientos de los artículos, tomando en cuenta cuáles se utilizan e incluso el orden en el que se utilizan. Para desarrollar esta etapa de la mejor manera es recomendable usar indicadores específicos en las áreas de trabajo, pudiendo ser etiquetas de uso, contorno de formas, codificación de colores, áreas de almacenamiento o similares de manera que se conozca qué artículos hay y en cuánta cantidad.
Indicadores de mejora que pueden observarse:
Para la aplicación de este paso a nivel de fábrica, se establece un estándar de limpieza para el lugar de trabajo y se implementan prácticas para mantenerlo limpio y ordenado en todo momento. Existen dos herramientas importantes que mejoran la implementación de esta etapa de manera significativa; la primera es la limpieza autónoma, la cual engloba la correcta limpieza de los equipos, indicando los materiales que se deben utilizar y cómo debe quedar cada elemento de la maquinaria. En segundo lugar tenemos la limpieza de los puestos; haciendo referencia a los residuos del área de trabajo (viruta, polvo, grasa) designando el cómo y con qué realizar estas limpiezas regulares.
Una manera de darle seguimiento a estas rutinas de limpieza puede ser utilizar hojas de registro o checklists para tener desglosadas las actividades a realizar y la periodicidad con la que deben hacerse.
Indicadores de mejora que pueden observarse:
Al momento de llegar a este paso es importante asegurarse de estandarizar los procesos que ya se implementaron anteriormente, y tratar de mantener estos estándares establecidos lo mejor posible. De ser necesario se recomienda utilizar el cuadro del ciclo de trabajo 5s para señalar visualmente las actividades y frecuencia que deben monitorearse. Asimismo, también puede aplicarse una lista de 5 puntos clave para valorar la organización, orden y limpieza por área y por puesto, de esta manera pueden detectarse puntos de mejora y acciones preventivas para continuar con el proceso.
Indicadores de mejora que pueden observarse:
En la última etapa, lo más importante es mantener y mejorar las prácticas establecidas en las etapas anteriores, de lo contrario los cambios no se verán reflejados en las áreas establecidas. Es de vital importancia para el puesto directivo promover una cultura de disciplina continua, ritmo y compromiso con la mejora continua en toda la organización.
Esto se consigue por medio de establecer sistemas de seguimiento y retroalimentación tales como buzón de sugerencias, pósters de las 5s o frases motivacionales que recuerden continuamente las metas de los cambios implementados.
Indicadores de mejora que pueden observarse:
Para implementar con éxito estas etapas 5’S en una organización manufacturera, es importante involucrar a todos los niveles de la empresa, desde la alta dirección hasta el personal de producción. Se deben proporcionar recursos adecuados, como capacitación y soporte técnico, y se deben establecer sistemas de seguimiento de estos recursos para medir de la mejor manera los resultados. Además, es crucial fomentar esta cultura de responsabilidad y propiedad entre los empleados, donde todos se sientan responsables de mantener un entorno de trabajo limpio, ordenado y seguro.
La filosofía japonesa de las 5’S ofrece un enfoque sistemático y efectivo para mejorar la eficiencia y la productividad en el lugar de trabajo. Las organizaciones manufactureras pueden crear un entorno de trabajo que fomente la excelencia operativa, la seguridad, la mejora continua e incluso la reducción de gasto innecesario de recursos. Recomiendo altamente priorizar estas prácticas porque he podido experimentar su implementación exitosa y posteriormente replicarla en mi entorno de trabajo.
¡Mantente al día con las últimas noticias y soluciones para el cuidado de tu empresa! Conoce sobre innovaciones que están transformando el mundo de la extracción industrial.