In industry, it is very common for the design and materials used in dust extraction duct systems to be downplayed. Usually, the concern is with the production machinery to which the extraction is applied and the dust collector, not so much with the methods of transporting the waste from point A to B. However, this journey is of paramount importance and , if manufactured or designed with the wrong materials, could have a significant impact on extraction results. Aspects such as the calculation of the diameters of the branches and their insertion in the main duct, as well as the radius of elbows and their deviations, are a core part of an efficient duct system, their improvisation or modification without technical parameters can lead to a waste of energy in the motor, in addition to a deficiency in the suction of the air.
To avoid this type of setback, it is essential to give the ducts the importance they deserve and see them as an essential part of the project, not a complement. So when we are about to acquire an extraction system, the main thing is to put it in the hands of professionals, but as a client you also have to validate that the project meets the basic requirements.
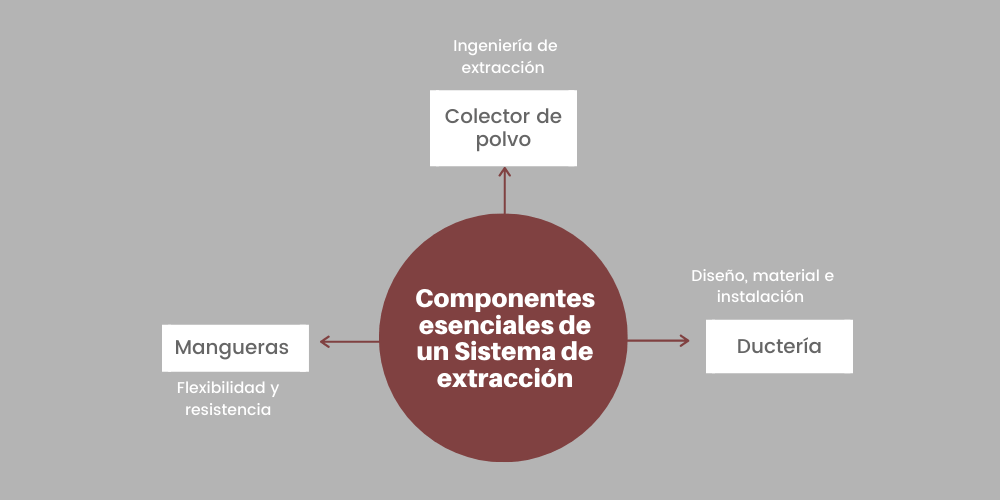
Materials and types of ducts available
- PVC ducts, elbows and reductions: The cheapest and easiest to obtain and install, but definitely the most dangerous. This material should not be used in dust extraction under any circumstances, as it is simply not designed for that purpose. When transporting materials in the air stream, PVC generates a lot of friction, which in turn creates a high static electrical charge, resulting in sparks. In this way we are not only running the risk of causing a fire, but also a spark that could damage the electronic control panels of our machinery. For all those who have already invested in machinery, it goes without saying how expensive this can be.
- Sheet spiroducts: The first thing worth noting is that for these ducts to obtain their shape, they must be manufactured with thin-gauge sheets, which makes them more sensitive to wear generated by friction when transporting abrasive materials. Secondly, their joints are engargoladas, which means that since they are not welded in their entirety, they could have weak assemblies. It is important to highlight these two points, since when it comes to extraction ducts, it must be remembered that they work at negative pressure and this effort applied to fragile ducts can result, in the worst case scenario, in a collapse of the facilities.
- Welded sheet ducts: Because they are welded, these ducts are made of galvanized sheet (generally) of thicker gauges (20 or 18), joined by flanges and screws. In appearance they may appear to be less aesthetic, but that loses importance when considering that their resistance is much higher, as is their useful life. They are manufactured in one-length sections according to a general plan and segmented into pieces that help their installation and transportation.
- Ducts with “fast clamp” system: Made of sheet metal, these ducts come in modular units and are joined with clamps that use the “fast clamp” methodology. Their use is becoming more and more popular since, in addition to presenting a solid construction, they facilitate and save their transfer and possible future modifications.
When it comes to an extraction system, there are many options and they represent a significant expense. For this reason, we recommend that when you decide to acquire one, you do so with the support of an expert who takes care of all its aspects and who, in addition, accompanies you once the installation is done to give the corresponding periodic maintenance. Otherwise, regardless of the size of the investment, the return will not be optimal.
More posts
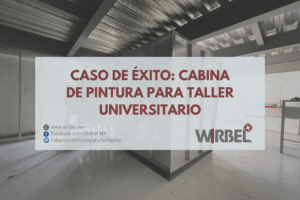
CASO DE ÉXITO: CABINA DE PINTURA PARA TALLER UNIVERSITARIO
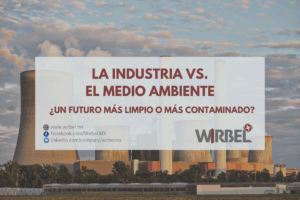
La Industria vs. El Medio Ambiente
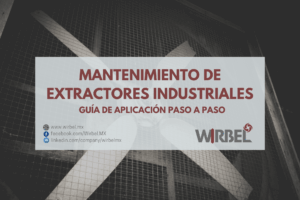
MANTENIMIENTO DE EXTRACTORES INDUSTRIALES
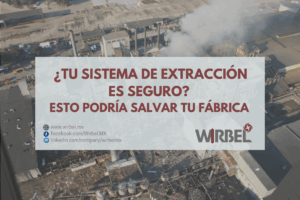